Технологія плавлення
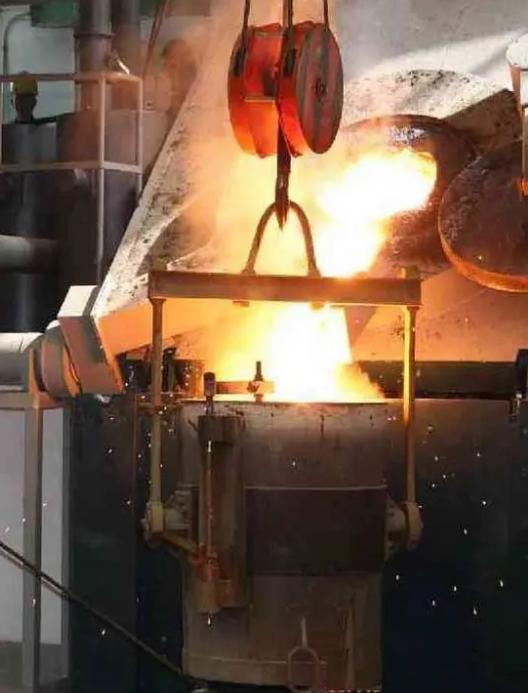
В даний час для плавлення продуктів переробки міді зазвичай використовують індукційну плавильну піч, а також плавку в ревербераційній печі та плавку в шахтній печі.
Плавка в індукційній печі підходить для всіх видів міді та мідних сплавів і має характеристики чистої плавки та забезпечення якості розплаву.За конструкцією печі індукційні печі поділяються на індукційні печі з сердечником і індукційні печі без сердечника.Індукційна піч із сердечником має характеристики високої ефективності виробництва та високої термічної ефективності та підходить для безперервного плавлення одного різновиду міді та мідних сплавів, таких як червона мідь та латунь.Індукційна піч без сердечника має характеристики швидкого нагріву та легкої заміни різновидів сплаву.Підходить для плавлення міді та мідних сплавів з високою температурою плавлення та різних різновидів, таких як бронза та мельхіор.
Вакуумна індукційна піч — це індукційна піч, оснащена вакуумною системою, придатною для плавлення міді та мідних сплавів, які легко вдихати та окислюватися, наприклад безкисневої міді, бериліївої бронзи, цирконієвої бронзи, магнієвої бронзи тощо для електричного вакууму.
Відбивна плавка в печі може очищати та видаляти домішки з розплаву, і в основному використовується для виплавки мідного брухту.Шахтова піч є різновидом швидкої безперервної плавильної печі, яка має переваги високої теплової ефективності, високої швидкості плавлення та зручного відключення печі.Можна контролювати;немає процесу рафінування, тому переважна більшість сировини повинна бути катодною міддю.Шахтові печі зазвичай використовуються з машинами безперервного лиття для безперервного лиття, а також можуть використовуватися з витримковими печами для напівбезперервного лиття.
Тенденція розвитку технології виробництва міді в основному відображається в зменшенні втрат сировини при горінні, зменшенні окислення та вдихання розплаву, покращенні якості розплаву та прийнятті високої ефективності (швидкість плавлення індукційної печі більша більше 10 т/год), великомасштабні (продуктивність індукційної печі може бути більше 35 т/комплект), довговічні (термін експлуатації футеровки 1-2 роки) та енергозберігаючі (енергоспоживання індукційної печі). піч становить менше 360 кВт·год/т), піч для витримки оснащена пристроєм для дегазації (дегазація газу CO), а індукційна піч. попередній нагрів печі, моніторинг стану печі та температурного поля вогнетривкої продукції та система сигналізації, утримуюча піч оснащена пристроєм для зважування, а контроль температури є більш точним.
Виробниче обладнання - Лінія різання
Виробництво лінії різання мідної смуги — це безперервна виробнича лінія для різання та різання, яка розширює широку котушку через розмотувач, розрізає рулон на необхідну ширину через машину для різання та перемотує її на кілька котушок через намотувач. (Стелаж для зберігання) Використовуйте кран для зберігання рулонів на стелажі
↓
(Завантажувальна машина) Використовуйте транспортний візок, щоб вручну помістити рулон матеріалу на барабан розмотувача та затягнути його
↓
(Розмотувач і притискний ролик, що запобігає ослабленню) Розмотайте котушку за допомогою відкриваючої напрямної та притискного ролика
↓
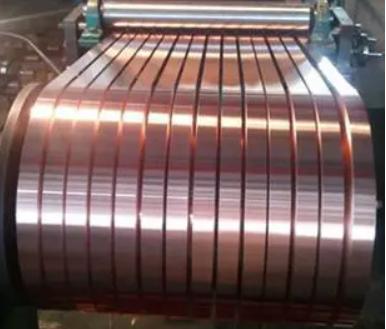
(NO·1 петельник і поворотний міст) зберігання та буфер
↓
(Направляюча кромка та пристрій притискного ролика) Вертикальні ролики спрямовують аркуш у притискні ролики, щоб запобігти відхиленню, ширина та положення вертикального направляючого ролика регулюються
↓
(Машина для різання) введіть машину для різання для позиціонування та різання
↓
(Швидкозмінне поворотне сидіння) Заміна групи інструментів
↓
(Пристрій для намотування брухту) Розріжте брухт
↓(Направляюча таблиця вихідного отвору та стопор хвоста котушки) Введення петельника №2
↓
(поворотний міст і петельник NO.2) зберігання матеріалу та усунення різниці товщини
↓
(Пристрій для натягу пресової пластини та сепараційного вала повітряного розширення) забезпечує силу натягу, відокремлення пластини та стрічки
↓
(Ножиці для різання, пристрій для вимірювання довжини рульового керування та направляючий стіл) вимірювання довжини, сегментація котушки з фіксованою довжиною, напрямна для заправки стрічки
↓
(намотувач, сепараційний пристрій, пристрій штовхальної пластини) сепараторна стрічка, намотування
↓
(розвантажувач, тара) мідна стрічка розвантаження та упаковка
Технологія гарячої прокатки
Гаряча прокатка в основному використовується для прокатки заготовок злитків для виробництва листів, смуг і фольги.
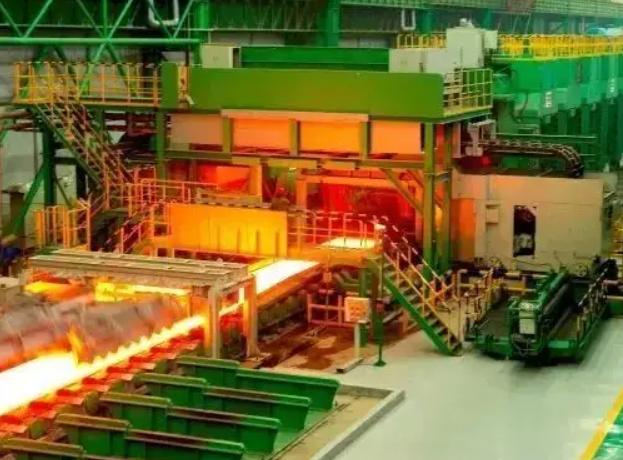
Специфікації зливків для прокатки заготовок повинні враховувати такі фактори, як різноманітність продукту, масштаб виробництва, метод лиття тощо, і пов’язані з умовами прокатного обладнання (такими як отвір валка, діаметр валка, допустимий тиск прокатки, потужність двигуна та довжина роликового столу) і т.д.Як правило, співвідношення між товщиною злитка та діаметром рулону становить 1: (3,5~7): ширина зазвичай дорівнює або в кілька разів перевищує ширину готового продукту, а ширина та розмір обрізки повинні бути належним чином розглядається.Як правило, ширина плити повинна становити 80% довжини тіла рулону.Довжина злитка повинна розумно враховуватися відповідно до умов виробництва.Взагалі кажучи, за умови, що кінцеву температуру гарячої прокатки можна контролювати, чим довший злиток, тим вище ефективність виробництва та вихід.
Специфікації зливка малих і середніх заводів з переробки міді зазвичай складають (60 ~ 150) мм × (220 ~ 450) мм × (2000 ~ 3200) мм, а вага зливка становить 1,5 ~ 3 т;специфікації зливка великих заводів з переробки міді. Зазвичай це (150~250) мм × (630~1250) мм × (2400~8000) мм, а вага зливка становить 4,5~20 т.
Під час гарячої прокатки температура поверхні валка різко підвищується в момент, коли валка контактує з високотемпературною прокаткою.Багаторазове теплове розширення і холодне стиснення викликають тріщини і тріщини на поверхні рулону.Тому під час гарячої прокатки необхідно проводити охолодження та змащування.Як охолоджувальне та мастильне середовище зазвичай використовується вода або емульсія меншої концентрації.Загальна робоча швидкість гарячої прокатки зазвичай становить від 90% до 95%.Товщина гарячекатаної стрічки зазвичай становить від 9 до 16 мм.Поверхневе фрезерування смуги після гарячої прокатки може видалити поверхневі оксидні шари, вкраплення окалини та інші поверхневі дефекти, що утворюються під час лиття, нагрівання та гарячої прокатки.Відповідно до тяжкості поверхневих дефектів гарячекатаної смуги та потреб процесу кількість фрезерування кожної сторони становить від 0,25 до 0,5 мм.
Стани гарячої прокатки, як правило, є реверсивними прокатними станами з двома або чотирма висотами.Зі збільшенням злитка та безперервним подовженням довжини смуги рівень керування та функції стану гарячої прокатки мають тенденцію постійного вдосконалення та вдосконалення, наприклад, використання автоматичного контролю товщини, гідравлічних згинальних валків, переднього та заднього вертикальні валки, лише охолоджувальні валки без охолодження. Пристрій прокатного пристрою, контроль корони TP roll (Taper Pis-ton Roll), онлайн-загартування (загартування) після прокатки, онлайн-намотування та інші технології для покращення однорідності структури та властивостей стрічки та отримання кращого плита.
Технологія лиття
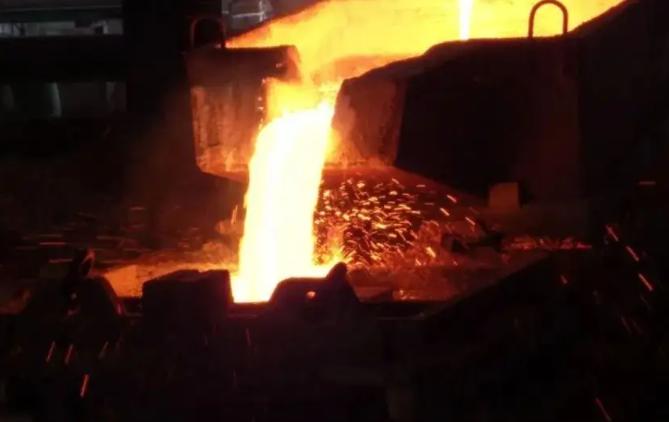
Лиття міді та мідних сплавів зазвичай поділяється на: вертикальне напівбезперервне лиття, вертикальне повне безперервне лиття, горизонтальне безперервне лиття, безперервне лиття вгору та інші технології лиття.
A. Вертикальне напівбезперервне лиття
Вертикальне напівбезперервне лиття має характеристики простого обладнання та гнучкого виробництва та підходить для лиття різноманітних круглих і плоских злитків міді та мідних сплавів.Режим передачі вертикальної машини напівбезперервного лиття поділяється на гідравлічний, ходовий гвинт і тросовий трос.Оскільки гідравлічна трансмісія є відносно стабільною, вона частіше використовується.За потреби кристалізатор може вібрувати з різними амплітудами та частотами.В даний час метод напівбезперервного лиття широко використовується у виробництві міді та мідних сплавів.
B. Вертикальне повне безперервне лиття
Вертикальне повне безперервне лиття має характеристики великої продуктивності та високого виходу (близько 98%), підходить для великомасштабного та безперервного виробництва зливків з одним сортом та специфікацією, і стає одним із основних методів вибору для плавлення та лиття. процес на сучасних великомасштабних лініях виробництва мідної стрічки.Вертикальна форма безперервного лиття має безконтактний лазерний автоматичний контроль рівня рідини.Ливарна машина, як правило, використовує гідравлічне затискання, механічну трансмісію, розпилювання сухої стружки з масляним охолодженням і збір стружки, автоматичне маркування та нахил злитка.Структура складна, а ступінь автоматизації високий.
C. Горизонтальне безперервне лиття
Горизонтальним безперервним литтям можна виготовляти заготовки та дротові заготовки.
Горизонтальним безперервним литтям смуги можна одержати стрічки з міді та мідних сплавів товщиною 14-20 мм.Смуги в цьому діапазоні товщини можна безпосередньо холоднокатати без гарячої прокатки, тому вони часто використовуються для виробництва сплавів, які важко піддаються гарячій прокатці (таких як олово, фосфориста бронза, свинцева латунь тощо), також можуть виготовляти латунь, стрічка з мельхіору та низьколегованого мідного сплаву.Залежно від ширини ливарної смуги горизонтальне безперервне лиття може відливати від 1 до 4 смуг одночасно.Зазвичай використовувані горизонтальні машини безперервного лиття можуть відливати одночасно дві смуги, кожна з шириною менше 450 мм, або відливати одну смугу з шириною смуги 650-900 мм.Горизонтальна стрічка безперервного лиття зазвичай використовує процес лиття тяга-зупинка-зворотний поштовх, і на поверхні є періодичні лінії кристалізації, які, як правило, слід усунути фрезеруванням.Існують вітчизняні зразки високоповерхневих мідних смуг, які можна виготовити методом волочіння та лиття смугових заготовок без фрезерування.
Горизонтальне безперервне лиття заготовок із труб, прутів і дроту може одночасно відливати від 1 до 20 зливків відповідно до різних сплавів і специфікацій.Як правило, діаметр прутка або дротяної заготовки становить від 6 до 400 мм, а зовнішній діаметр трубної заготовки становить від 25 до 300 мм.Товщина стінки 5-50 мм, довжина сторони злитка 20-300 мм.Переваги методу горизонтального безперервного лиття полягають у тому, що процес короткий, виробничі витрати низькі, а ефективність виробництва висока.У той же час, це також необхідний метод виробництва для деяких сплавів з поганою гарячою оброблюваністю.Останнім часом це основний спосіб виготовлення заготовок із широко використовуваних мідних виробів, таких як смуги олов’яно-фосфорної бронзи, смуги з цинк-нікелевих сплавів і труби для кондиціонування повітря з розкисленої фосфором міді.методи виробництва.
Недоліками методу виробництва горизонтального безперервного лиття є: відповідні різновиди сплаву є відносно простими, витрата графітового матеріалу у внутрішній гільзі форми є відносно великою, а однорідність кристалічної структури поперечного перерізу зливка не є легко контролювати.Нижня частина злитка безперервно охолоджується завдяки дії сили тяжіння, яка наближена до внутрішньої стінки виливниці, і зерна більш дрібні;верхня частина обумовлена утворенням повітряних проміжків і високою температурою розплаву, що викликає затримку затвердіння злитка, що уповільнює швидкість охолодження і створює гістерезис затвердіння зливка.Кристалічна структура відносно груба, що особливо помітно для великих злитків.Зважаючи на зазначені вище недоліки, в даний час розробляється метод лиття заготовкою по вертикальному гнуттю.Німецька компанія використовувала безперервну машину для лиття з вертикальним згином для випробування лиття (16-18) мм × 680 мм смуг олов’яної бронзи, таких як DHP і CuSn6, зі швидкістю 600 мм/хв.
D. Безперервне лиття вгору
Безперервне лиття вгору – це технологія лиття, яка швидко розвивалася за останні 20-30 років і широко використовується у виробництві дротяних заготовок для яскравої мідної катанки.Він використовує принцип лиття під вакуумним всмоктуванням і застосовує технологію зупинки-витягування для реалізації безперервного лиття з кількома головками.Він має характеристики простого обладнання, невеликих інвестицій, менших втрат металу та низьких процедур забруднення навколишнього середовища.Безперервне лиття вгору зазвичай підходить для виробництва червоної міді та заготовок з безкисневої міді.Новим досягненням останніх років є його популяризація та застосування в трубних заготовках великого діаметру, латуні та мельхіорі.В даний час розроблена установка безперервного лиття вгору продуктивністю 5000 т на рік і діаметром більше Φ100 мм;двійкові звичайні латуні та цинк-біла мідь потрійного сплаву заготовки були виготовлені, і вихід заготовок дроту може досягати більше 90%.
E. Інші техніки лиття
Розробляється технологія безперервного лиття заготовок.Він усуває такі дефекти, як сліди від волокон, що утворилися на зовнішній поверхні заготовки внаслідок процесу зупинки-витягування безперервного лиття вгору, і якість поверхні є чудовою.А завдяки характеристикам майже спрямованого затвердіння внутрішня структура є більш однорідною та чистою, тому продуктивність продукту також краща.Технологія виробництва стрічкового безперервного лиття заготовок з мідного дроту широко використовується на великих виробничих лініях понад 3 тонни.Площа поперечного перерізу плити, як правило, перевищує 2000 мм2, і за нею йде безперервний прокатний стан із високою ефективністю виробництва.
Електромагнітне лиття було випробувано в моїй країні ще в 1970-х роках, але промислове виробництво не було реалізовано.За останні роки технологія електромагнітного лиття досягла значного прогресу.В даний час успішно відливаються злитки безкисневої міді Φ200 мм з гладкою поверхнею.У той же час перемішувальний вплив електромагнітного поля на розплав може сприяти видаленню вихлопних газів і шлаку, і можна отримати безкисневу мідь із вмістом кисню менше 0,001%.
Напрямок нової технології лиття мідного сплаву полягає в покращенні структури форми за допомогою спрямованого затвердіння, швидкого затвердіння, напівтвердого формування, електромагнітного перемішування, метаморфічної обробки, автоматичного контролю рівня рідини та інших технічних засобів відповідно до теорії затвердіння., ущільнення, очищення та реалізація безперервної роботи та формування ближнього кінця.
У довгостроковій перспективі лиття міді та мідних сплавів буде співіснувати технологія напівбезперервного лиття та технологія повного безперервного лиття, а частка застосування технології безперервного лиття буде продовжувати збільшуватися.
Технологія холодної прокатки
Відповідно до специфікації рулонної смуги та процесу прокатки холодна прокатка підрозділяється на обжимну, проміжну та чистову прокатку.Процес холодної прокатки литої смуги товщиною від 14 до 16 мм і гарячекатаної заготовки товщиною приблизно від 5 до 16 мм до 2 - 6 мм називається розкачуванням, а процес продовження зменшення товщини Прокату називають проміжною прокаткою.Остаточна холодна прокатка для задоволення вимог готового продукту називається чистовою прокаткою.
У процесі холодної прокатки необхідно контролювати систему скорочення (загальну швидкість обробки, швидкість проходження обробки та швидкість обробки готового продукту) відповідно до різних сплавів, специфікацій прокатки та вимог до продуктивності готової продукції, розумно вибирати та регулювати форму валків, а також розумно вибирати змащення спосіб і мастило.Вимірювання та регулювання натягу.
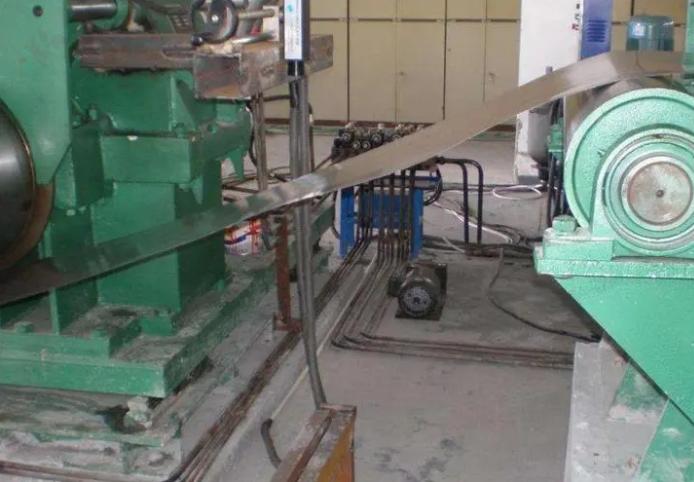
Стани холодної прокатки зазвичай використовують реверсивні прокатні стани з чотирма або кількома висотами.Сучасні стани холодної прокатки зазвичай використовують низку технологій, таких як гідравлічне позитивне та негативне згинання валків, автоматичний контроль товщини, тиску та натягу, осьовий рух валків, сегментне охолодження валків, автоматичний контроль форми листа та автоматичне вирівнювання прокату. , щоб можна було підвищити точність смуги.До 0,25±0,005 мм і в межах 5I форми пластини.
Тенденція розвитку технології холодної прокатки відображається в розробці та застосуванні високоточних багатовалкових станів, вищих швидкостей прокатки, більш точного контролю товщини та форми смуги, а також допоміжних технологій, таких як охолодження, змащування, намотування, центрування та швидка прокатка. змінити.доопрацювання та ін.
Виробниче Обладнання - Колпак
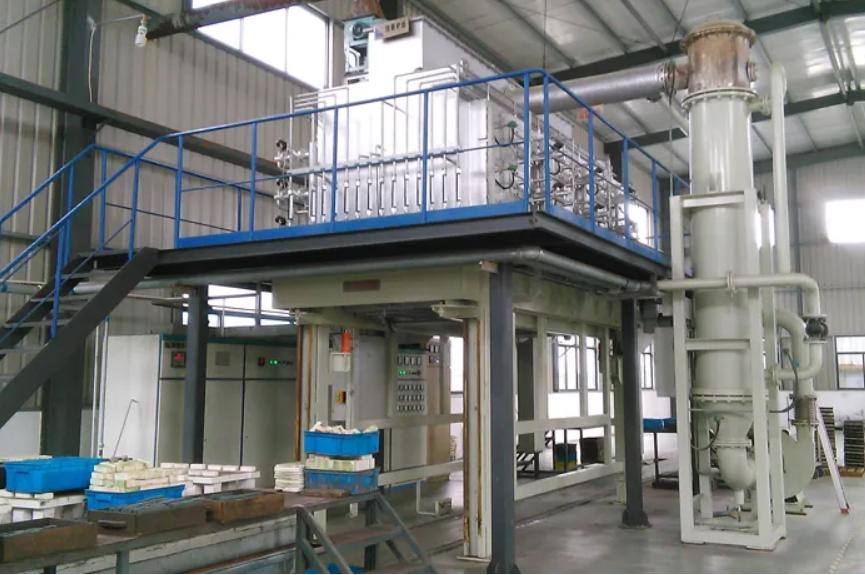
Дзвонові та підйомні печі зазвичай використовуються в промисловому виробництві та дослідних випробуваннях.Як правило, потужність велика, а споживання енергії велике.Для промислових підприємств матеріалом печі підйомної печі Luoyang Sigma є керамічне волокно, яке має хороший енергозберігаючий ефект, низьке споживання енергії та низьке споживання енергії.Економія електроенергії та часу, що вигідно для збільшення виробництва.
Двадцять п'ять років тому німецькі BRANDS і Philips, провідна компанія у галузі виробництва феритів, спільно розробили нову агломераційну машину.Розробка цього обладнання відповідає особливим потребам феритової промисловості.Під час цього процесу BRANDS Bell Furnace постійно оновлюється.
Він звертає увагу на потреби всесвітньо відомих компаній, таких як Philips, Siemens, TDK, FDK тощо, які також виграють від високоякісного обладнання BRANDS.
Завдяки високій стабільності продуктів, вироблених дзвоновими печами, дзвонові печі стали провідними компаніями в промисловості професійного виробництва феритів.Двадцять п’ять років тому перша піч виробництва BRANDS все ще виробляє високоякісні продукти для Philips.
Основною характеристикою печі для спікання, пропонованої дзвоновою піччю, є її висока ефективність.Його інтелектуальна система управління та інше обладнання утворюють повну функціональну одиницю, яка може повністю відповідати майже найсучаснішим вимогам феритової промисловості.
Клієнти колпакових печей можуть програмувати та зберігати будь-який температурний/атмосферний профіль, необхідний для виробництва високоякісної продукції.Крім того, клієнти також можуть виробляти будь-які інші продукти вчасно відповідно до фактичних потреб, тим самим скорочуючи час виконання та знижуючи витрати.Обладнання для агломерації повинно мати хороші налаштування, щоб виробляти різноманітні продукти, щоб постійно адаптуватися до потреб ринку.Це означає, що відповідна продукція повинна виготовлятися відповідно до потреб індивідуального замовника.
Хороший виробник феритів може виготовити понад 1000 різних магнітів для задоволення особливих потреб клієнтів.Вони вимагають здатності повторити процес спікання з високою точністю.Системи дзвонових печей стали стандартними печами для всіх виробників фериту.
У феритовій промисловості ці печі в основному використовуються для низького енергоспоживання та високого значення μ, особливо в галузі зв’язку.Без дзвонової печі неможливо виготовити якісні стрижні.
Дзвонова піч потребує лише кількох операторів під час спікання, завантаження та розвантаження можна завершити вдень, а спікання можна завершити вночі, що дозволяє зменшити пік електроенергії, що дуже практично в сучасній ситуації дефіциту електроенергії.Дзвонові печі виробляють продукцію високої якості, а всі додаткові вкладення швидко окупаються завдяки якісній продукції.Контроль температури та атмосфери, конструкція печі та контроль повітряного потоку всередині печі ідеально інтегровані для забезпечення рівномірного нагріву та охолодження продукту.Контроль атмосфери печі під час охолодження безпосередньо пов’язаний з температурою печі та може гарантувати вміст кисню 0,005% або навіть нижче.А це те, чого наші конкуренти не можуть зробити.
Завдяки повній системі введення алфавітно-цифрового програмування можна легко відтворити тривалі процеси спікання, що забезпечує якість продукції.Продаж товару також є відображенням його якості.
Технологія термічної обробки
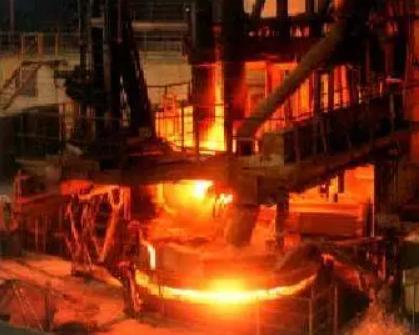
Декілька злитків сплаву (смуг) із сильним розшаруванням дендритів або ливарною напругою, таких як олов’яно-фосфорна бронза, потребують спеціального гомогенізаційного відпалу, який зазвичай виконується в колпаковій печі.Температура гомогенізаційного відпалу зазвичай становить від 600 до 750 °C.
В даний час більшість проміжного відпалу (рекристалізаційний відпал) і кінцевого відпалу (відпал для контролю стану та характеристик виробу) смуг мідного сплаву піддаються яскравому відпалу за допомогою газового захисту.Типи печей включають колпачкову піч, піч на повітряній подушці, піч з вертикальною тягою тощо. Окислювальний відпал поступово припиняється.
Тенденція розвитку технології термічної обробки відображена в гарячій прокатці в режимі он-лайн обробки розчином дисперсійно зміцнених сплавів і подальшої технології термічної обробки деформації, безперервного яскравого відпалу та відпалу натягу в захисній атмосфері.
Загартування — термічна обробка старінням в основному використовується для термообробленого зміцнення мідних сплавів.Завдяки термічній обробці продукт змінює свою мікроструктуру і набуває необхідних властивостей.З розвитком високоміцних і високопровідних сплавів процес термічної обробки загартуванням і старінням буде більш застосованим.Обладнання для обробки старінням приблизно таке ж, як обладнання для відпалу.
Технологія екструзії
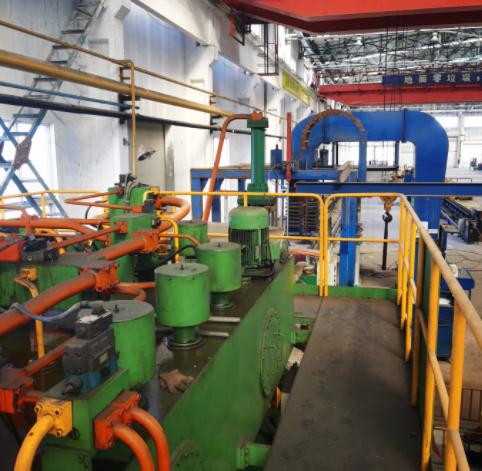
Екструзія — це зрілий і вдосконалений метод виробництва труб, стрижнів, профілів і постачання заготовок з міді та мідних сплавів.Змінюючи матрицю або використовуючи метод перфораційної екструзії, різні сорти сплавів і різні форми поперечного перерізу можуть бути безпосередньо екструдовані.За допомогою екструзії лита структура злитка змінюється на оброблену структуру, а екструдована трубна заготовка та заготовка прутків мають високу точність розмірів, а структура є тонкою та однорідною.Метод екструзії - це метод виробництва, який зазвичай використовують вітчизняні та іноземні виробники мідних труб і стрижнів.
Кування мідних сплавів в основному здійснюється виробниками машин у моїй країні, в основному включаючи вільне кування та штампування, таких як великі шестерні, черв’ячні шестерні, черв’яки, зубчасті кільця автомобільних синхронізаторів тощо.
Метод екструзії можна розділити на три види: пряма екструзія, зворотна екструзія та спеціальна екструзія.Серед них є багато застосувань прямої екструзії, зворотна екструзія використовується у виробництві малих і середніх стрижнів і дроту, а спеціальна екструзія використовується в спеціальному виробництві.
Під час екструдування, відповідно до властивостей сплаву, технічних вимог до екструдованих виробів, а також потужності та конструкції екструдера, тип, розмір і коефіцієнт екструзії злитка повинні бути розумно обрані, щоб ступінь деформації був не менше 85%.Температура екструзії та швидкість екструзії є основними параметрами процесу екструзії, і прийнятний діапазон температур екструзії повинен визначатися відповідно до діаграми пластичності та фазової діаграми металу.Для міді та мідних сплавів температура екструзії зазвичай становить від 570 до 950 °C, а температура екструзії міді досягає навіть 1000-1050 °C.У порівнянні з температурою нагрівання екструзійного циліндра від 400 до 450 °C, різниця температур між ними є відносно високою.Якщо швидкість екструзії надто повільна, температура поверхні злитка впаде занадто швидко, що призведе до збільшення нерівномірності потоку металу, що призведе до збільшення навантаження екструзії та навіть спричинить явище розточування .Тому для міді та мідних сплавів зазвичай використовується відносно високошвидкісна екструзія, швидкість екструзії може досягати понад 50 мм/с.
При екструдуванні міді та мідних сплавів для видалення поверхневих дефектів злитка часто використовують відшаровувальну екструзію, товщина відшаровування становить 1-2 мкм.Водне ущільнення зазвичай використовується на виході екструзійної заготовки, щоб продукт можна було охолодити в резервуарі для води після екструзії, а поверхня продукту не окислювалася, а подальшу холодну обробку можна проводити без травлення.Він має тенденцію використовувати великотоннажний екструдер із синхронним приймальним пристроєм для екструдування рулонів труб або дроту з одноразовою вагою понад 500 кг, щоб ефективно підвищити ефективність виробництва та повний вихід наступної послідовності.В даний час виробництво труб з міді та мідних сплавів переважно використовує горизонтальні гідравлічні екструдери вперед з незалежною системою перфорації (подвійної дії) і прямою передачею масляного насоса, а виробництво прутків переважно використовує незалежну систему перфорації (одинарної дії) і масляний насос прямої передачі.Горизонтальний гідравлічний екструдер прямого або зворотного ходу.Специфікації екструдера, що зазвичай використовуються, становлять 8-50 МН, і зараз його, як правило, виробляють великотоннажними екструдерами понад 40 МН, щоб збільшити вагу одного злитка, тим самим покращуючи ефективність виробництва та вихід.
Сучасні горизонтальні гідравлічні екструдери конструктивно оснащені попередньо напруженою цілісною рамою, направляючою та опорою екструзійного барабана «X», вбудованою системою перфорації, внутрішнім охолодженням перфораційної голки, набором ковзних або обертових матриць і пристроєм для швидкої зміни матриці, потужним змінним масляним насосом прямої дії привід, інтегрований логічний клапан, керування ПЛК та інші передові технології, обладнання має високу точність, компактну структуру, стабільну роботу, безпечне блокування та простий у реалізації програмний контроль.Технологія безперервної екструзії (Conform) досягла певного прогресу за останні десять років, особливо для виробництва прутів спеціальної форми, таких як дріт для електровозів, що є дуже перспективним.В останні десятиліття нові технології екструзії швидко розвиваються, і тенденція розвитку технології екструзії втілюється в наступному: (1) Екструзійне обладнання.Сила екструзії екструзійного преса розвиватиметься в більшому напрямку, і екструзійний прес понад 30 МН стане основним корпусом, а автоматизація виробничої лінії екструзійного преса продовжуватиме вдосконалюватися.Сучасні екструзійні машини повністю адаптували комп’ютерне програмне керування та програмоване логічне керування, завдяки чому ефективність виробництва значно покращилася, кількість операторів значно зменшилася, і навіть можна реалізувати автоматичну безпілотну роботу екструзійних виробничих ліній.
Конструкція корпусу екструдера також постійно вдосконалювалася та вдосконалювалася.В останні роки деякі горизонтальні екструдери прийняли попередньо напружену раму для забезпечення стабільності загальної конструкції.Сучасний екструдер реалізує пряму і зворотну методи екструзії.Екструдер оснащений двома екструзійними валами (основний екструзійний вал і вал матриці).Під час екструзії екструзійний циліндр рухається разом з головним валом.У цей час продукт є Напрямок витікання узгоджується з напрямком руху головного валу та протилежний відносному напрямку руху осі матриці.Основа матриці екструдера також приймає конфігурацію кількох станцій, що не тільки полегшує зміну матриці, але й підвищує ефективність виробництва.У сучасних екструдерах використовується лазерний пристрій контролю відхилення, який надає ефективні дані про стан центральної лінії екструзії, що зручно для своєчасного та швидкого регулювання.Гідравлічний прес з насосом високого тиску з прямим приводом, що використовує масло як робоче середовище, повністю замінив гідравлічний прес.Екструзійні інструменти також постійно оновлюються з розвитком технології екструзії.Голка для пірсингу з внутрішнім водяним охолодженням широко просувається, а голка для проколювання та прокатки зі змінним поперечним перерізом значно покращує ефект змащення.Більш широко використовуються керамічні форми та форми з легованої сталі з тривалим терміном служби та вищою якістю поверхні.
Екструзійні інструменти також постійно оновлюються з розвитком технології екструзії.Голка для пірсингу з внутрішнім водяним охолодженням широко просувається, а голка для проколювання та прокатки зі змінним поперечним перерізом значно покращує ефект змащення.Застосування керамічних форм і форм із легованої сталі з більшим терміном служби та вищою якістю поверхні є більш популярним.(2) Процес виробництва екструзії.Різновиди та специфікації екструдованих виробів постійно розширюються.Екструзія труб, стрижнів, профілів і надвеликих профілів малого перерізу надвисокої точності забезпечує якість зовнішнього вигляду виробів, зменшує внутрішні дефекти виробів, зменшує геометричні втрати та сприяє подальшому розвитку методів екструзії, таких як рівномірна продуктивність екструдованого продуктів.Також широко використовується сучасна технологія зворотної екструзії.Для металів, які легко окислюються, використовується екструзія гідрозатвору, яка може зменшити забруднення травленням, зменшити втрати металу та покращити якість поверхні виробів.Для екструдованих продуктів, які потрібно загартувати, просто контролюйте відповідну температуру.Метод екструзії водяного ущільнення може досягти мети, ефективно скоротити виробничий цикл і заощадити енергію.
З безперервним удосконаленням потужності екструдера та технології екструзії поступово застосовуються сучасні технології екструзії, такі як ізотермічна екструзія, екструзія з охолоджувальною головкою, високошвидкісна екструзія та інші технології прямої екструзії, зворотна екструзія, гідростатична екструзія Практичне застосування технології безперервної екструзії пресування та конформування, застосування технології екструзії порошку та багатошарової композитної екструзії низькотемпературних надпровідних матеріалів, розробка нових методів, таких як екструзія напівтвердого металу та багатозаготовкова екструзія, розробка невеликих точних деталей, технологія формування холодної екструзії, і т.д., були швидко розроблені та широко розроблені та застосовані.
спектрометр
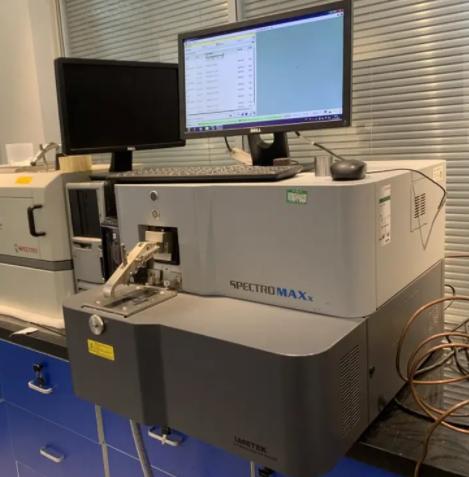
Спектроскоп — науковий прилад, який розкладає світло складного складу на спектральні лінії.Семикольорове світло в сонячному світлі — це частина, яку можна розрізнити неозброєним оком (видиме світло), але якщо сонячне світло розкласти за допомогою спектрометра та впорядкувати за довжиною хвилі, видиме світло займає лише невеликий діапазон у спектрі, а решта — спектри, які неможливо розрізнити неозброєним оком, такі як інфрачервоні промені, мікрохвилі, ультрафіолетові промені, рентгенівські промені тощо. Оптична інформація фіксується спектрометром, проявляється за допомогою фотоплівки або відображається й аналізується комп’ютеризованим автоматичним дисплеєм числовий інструмент, щоб визначити, які елементи містяться в статті.Ця технологія широко використовується для виявлення забруднення повітря, забруднення води, харчової гігієни, металургійної промисловості тощо.
Спектрометр, також відомий як спектрометр, широко відомий як спектрометр прямого зчитування.Пристрій, який вимірює інтенсивність спектральних ліній на різних довжинах хвиль за допомогою фотоприймачів, таких як фотоелектронні помножувачі.Він складається з вхідної щілини, дисперсійної системи, системи зображення та однієї або кількох вихідних щілин.Електромагнітне випромінювання джерела випромінювання розділяється на необхідну довжину хвилі або область довжин хвиль дисперсійним елементом, і інтенсивність вимірюється на обраній довжині хвилі (або сканування певної смуги).Існує два види монохроматорів і поліхроматорів.
Тестовий прилад-кондуктометр
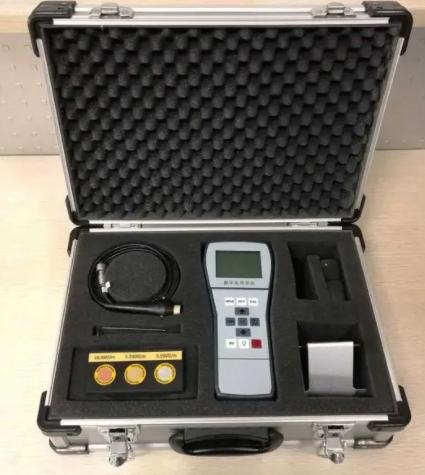
Цифровий ручний тестер провідності металу (кондуктометр) FD-101 застосовує принцип виявлення вихрових струмів і спеціально розроблений відповідно до вимог провідності електротехнічної промисловості.Він відповідає стандартам випробувань металургійної промисловості щодо функціональності та точності.
1. Вихрострумовий кондуктометр ФД-101 має три унікальних:
1) Єдиний китайський кондуктометр, який пройшов перевірку Інституту аеронавігаційних матеріалів;
2) Єдиний китайський кондуктометр, який може задовольнити потреби компаній авіабудування;
3) Єдиний китайський кондуктометр, який експортується в багато країн.
2. Введення функції продукту:
1) Великий діапазон вимірювання: 6,9% IACS-110% IACS (4,0 мс/м-64 мс/м), що відповідає тесту електропровідності всіх кольорових металів.
2) Інтелектуальне калібрування: швидке й точне, повністю уникаючи помилок калібрування вручну.
3) Прилад має хорошу температурну компенсацію: показання автоматично компенсуються до значення при 20 °C, і на корекцію не впливає людська помилка.
4) Гарна стабільність: це ваш особистий охоронець для контролю якості.
5) Гуманізоване інтелектуальне програмне забезпечення: воно надає вам зручний інтерфейс виявлення та потужні функції обробки та збору даних.
6) Зручна експлуатація: виробничий майданчик і лабораторію можна використовувати всюди, завоювавши прихильність більшості користувачів.
7) Самозаміна зондів: кожен хост може бути оснащений кількома зондами, і користувачі можуть замінити їх у будь-який час.
8) Числова роздільна здатність: 0,1% IACS (MS/m)
9) Інтерфейс вимірювання одночасно відображає значення вимірювань у двох одиницях %IACS і MS/m.
10) Він має функцію зберігання даних вимірювань.
Твердомір
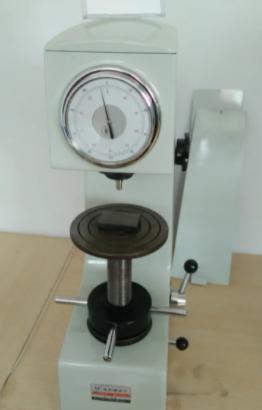
Інструмент має унікальний і точний дизайн у механіці, оптиці та джерелі світла, що робить зображення відступу чіткішим, а вимірювання точнішим.У вимірюванні можуть брати участь як 20-кратні, так і 40-кратні лінзи об’єктивів, що робить діапазон вимірювання більшим, а застосування більш широким.Прилад оснащений цифровим вимірювальним мікроскопом, який може відображати метод випробування, випробувальне зусилля, довжину відбитка, значення твердості, час утримання випробувального зусилля, час вимірювання тощо на рідкому екрані, і має різьбовий інтерфейс, який можна підключити до цифрової камери та камери CCD.Має певну репрезентативність у вітчизняній головній продукції.
Тестовий прилад-детектор питомого опору
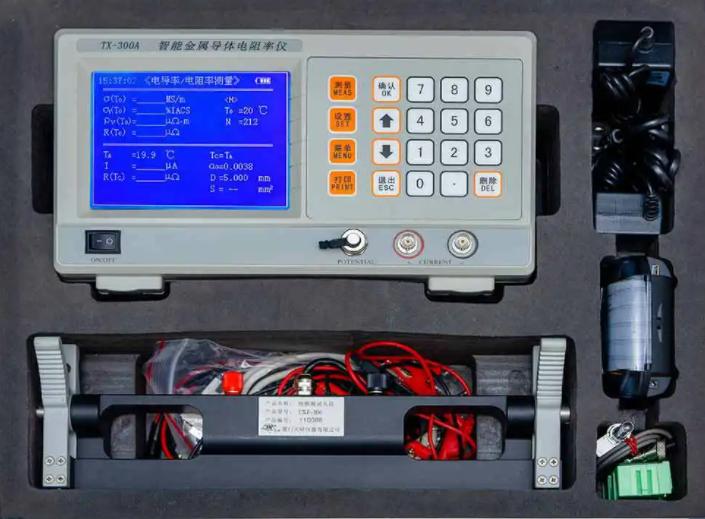
Прилад для вимірювання питомого опору металевого дроту є високоефективним інструментом для вимірювання таких параметрів, як питомий опір дроту, стрижня та електропровідність.Його продуктивність повністю відповідає відповідним технічним вимогам GB/T3048.2 і GB/T3048.4.Широко використовується в металургії, електроенергетиці, проводах і кабелях, електроприладах, коледжах і університетах, науково-дослідних підрозділах та інших галузях промисловості.
Основні характеристики інструменту:
(1) Він об’єднує передові електронні технології, однокристальні технології та технологію автоматичного виявлення, з сильною функцією автоматизації та простим керуванням;
(2) Просто натисніть клавішу один раз, усі виміряні значення можна отримати без будь-яких розрахунків, що підходить для постійного, швидкого та точного виявлення;
(3) Конструкція з живленням від батареї, невеликий розмір, легкий у транспортуванні, підходить для польового та польового використання;
(4) Великий екран, великий шрифт, може одночасно відображати питомий опір, провідність, опір та інші вимірювані значення та температуру, випробувальний струм, коефіцієнт температурної компенсації та інші допоміжні параметри, дуже інтуїтивно зрозумілі;
(5) Одна машина є багатоцільовою, має 3 інтерфейси вимірювання, а саме інтерфейс вимірювання питомого опору провідника та провідності, інтерфейс комплексного вимірювання параметрів кабелю та інтерфейс вимірювання опору постійного струму кабелю (тип TX-300B);
(6) Кожне вимірювання має функції автоматичного вибору постійного струму, автоматичної комутації струму, автоматичної корекції нульової точки та автоматичної корекції температурної компенсації для забезпечення точності кожного значення вимірювання;
(7) Унікальне портативне випробувальне пристосування з чотирма клемами підходить для швидкого вимірювання різних матеріалів і різних специфікацій дротів або прутків;
(8) Вбудована пам'ять даних, яка може записувати та зберігати 1000 наборів даних вимірювань і параметрів вимірювання, а також підключатися до верхнього комп'ютера для створення повного звіту.